- Home
- Technology
TECHNOLOGY
We think "Repeatability"
is the key
for technology and quality
of our products.
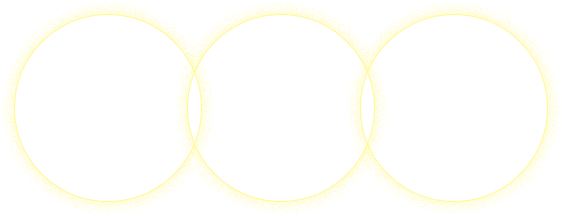
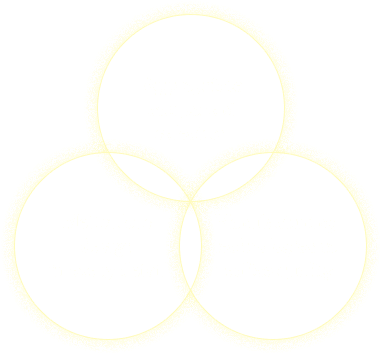
What SHINKO can do
Springs (sometimes over 1 million pieces per month with tight tolerances) are made through processes below.
- WireFeeding
- WireCoiling
- WireBending
- WireCutting
Our consept of repeatability contributes to realization of customers' expectation in all the processes.
What SHINKO can give
"Added Value" of high precision of each spring, "Trust and Security" of continuous production with the same shape.
The produced "springs" are eventually combined with other parts, and demonstrate their good performance.
SHINKO gives through
- Manufacturing methods(Machines, Tools)
- After-sales Service(Maintenance, Training)
"Added-Value" and "Trust and Security" to Customers' production site.
Repeatability
means
Continuing to produce high-precision springs with the same shape from the first to the millionth.
To realize this "Repeatability,"
- ・We work on each of the processes below with careful attention.
- ・Designing based on spring making theory
- ・Making parts drawings and Choosing purchased parts
- ・Inspecting the parts
- ・Quality relization process through assembling the parts to units or machines
- ・Testing completed machine products
SHINKO's manufacturing is a manufacturing that customers feel the quality difference after 5 to 10 year use of our products.
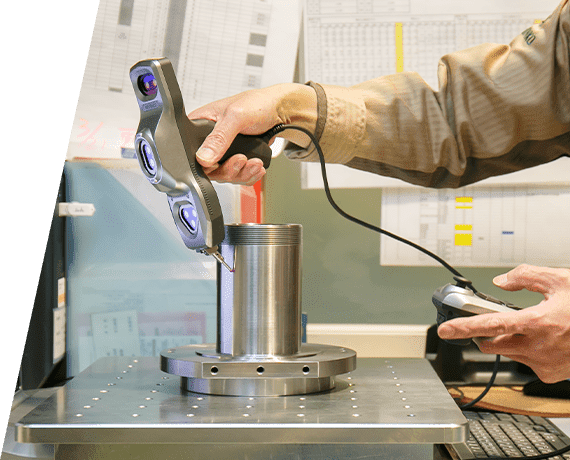
Triggers for
New Products
We plan our products by ourselves. There are three triggers for new products.
- 1. Products from customer's request
- 2. Successor products with new technologies
- 3. Products from our own desire and ideas
Thinking from "Springs" is important for new products.
- ・How to realize shapes and quality
- ・Influence to springs and operability after adopting new technologies
- ・How our ambition works for customer's spring production
Considering matters above, we discuss, experiment, plan, and realize new products. This is the most important and most interesting jobs for SHINKO, a machine manufacturer.
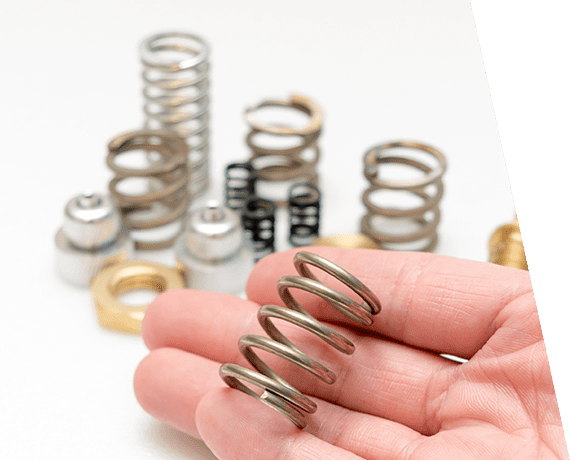
ZF series was born from our ambition.
Many domestic and global spring manufacturers had had impression that SHINKO's extension machines are good, but they do not know SHINKO's torsion machines well. We wanted to dispell this reputation and made many discussion with strong wish to surprise visitors of exhibitions by releasing the world-best torsion machine. The wish and discussion brought ideas such as "3 3D servo slides" and "Spindle changer", which gave us good evaluation in its functions, wide manufacturing area and durability, and gave many sales achievement in both domestic and global markets.
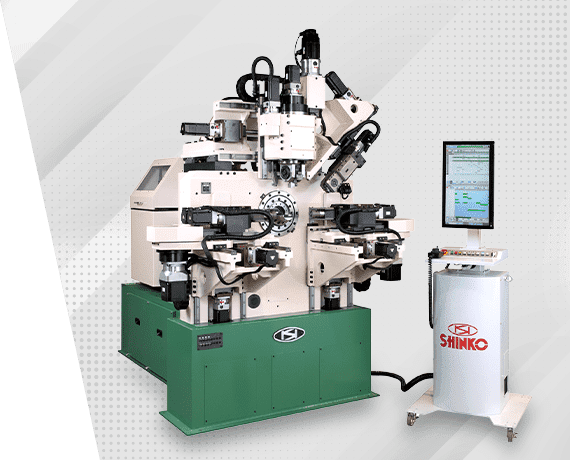
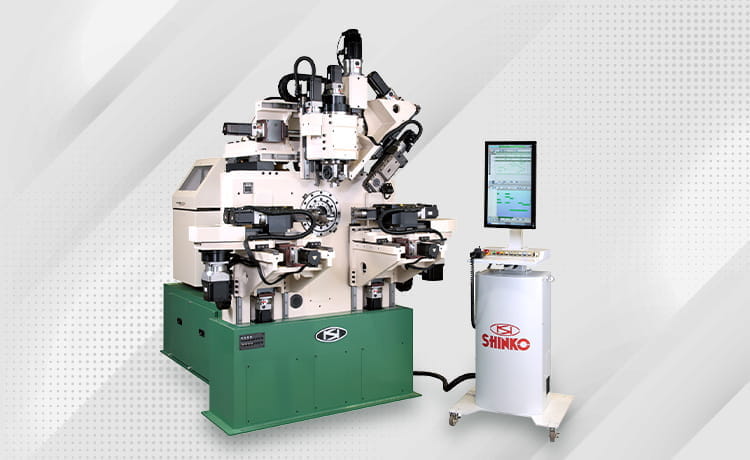
Production Process
Production Process
-
STEP01 Planning and Designing
Once the "product planning" (= what kind of value should be delivered to customers) is decided, "development design" is started. "Designing" is the key to product function, performance, quality, and cost. With "Realization of Repeatability" in mind, we discuss with other departments and suppliers to shape our ideas into basic design, detailed design, and parts design.
-
STEP02 Procurement, Manufacturing Process and Manufacturing technologies
Based on the parts list, we request quotations and place orders with suppliers. We discuss with the partners to make the best use of their excellent processing technologies and know-how. Considering the delivery date and our whole production schedule, we decide the assembly process and the person in charge. Especially for the first new machine, we try to build the optimum manufacturing process at the same time.
-
STEP03 Making parts, Inspection
Some parts are also manufactured in-house. Inspection of parts with 1/100mm dimesion tolerance is an important and sensitive task. We carefully proceed one by one with the awareness that "Quality starts with parts" sometimes using 3D inspection equipment.
-
STEP04 Assembling units
Assembly is not just assembly, but "the final process to achieve quality". In our company, one or two manufacturing engineers are in charge of whole assembly process which is called "Cell Production." Even if the parts meet design tolerances, it is sometimes necessary to make fine finihsing on-site during the assembly process such as adjustment of accumulated tolerance of combined parts, the smoothness of sliding surfaces, and the pressurization of bearings. We work carefully one by one here so that customers can feel the difference in 5 or 10 years.
-
STEP05 Completion
Connecting the electrical components is the final process. We check for minor omissions and mistakes, and perform a final test to see if the machine works as intended. We sometimes assemble safety covers and sensors. In the case of the first machine and modified machines, our development and design team will actually make springs and perform performance tests. Contracted customers sometimes come for inspection and training. I'm nervous, but it's also a happy moment to see the faces of the customers who will use it.